The Onkalo nuclear waste disposal facility under construction in Olkiluoto, Finland, will be the world’s first permanent geological repository for spent nuclear fuel and high-level radioactive waste. Posiva is using a Scanclimber hybrid hoist-work platform SC2000 in assembly work inside the personnel shaft in Onkalo. The product was custom-built according to Posiva’s requirements. The SC2000 hoist-work platform is a hybrid of a hoist and a mast climber (MCWP).
The site
Jarno Säippä is the project manager at Posiva’s (www.posiva.fi) Final disposal – project. He has worked in the mining industry in various positions and is now responsible for the project shaft construction.
The first time I came to the Posiva Onkalo construction site in 2006, I was employed by a mining contractor. I have also previously worked at the gold mine and as the inspector for STUK (Radiation and Nuclear Safety Authority of Finland) to supervise this construction site.
Onkalo is a unique project, the first of its kind in the world. The International Atomic Energy Agency’s (IAEA) general director called Onkalo
A game-changer for the long-term sustainability of nuclear energy.

The Onkalo spent nuclear fuel repository is planned for the final disposal of spent nuclear fuel. It is located near the Olkiluoto Nuclear Power Plant in the municipality of Eurajoki, on the west coast of Finland. Posiva is constructing it, and the concept is based on the KBS-3 method of nuclear waste burial developed in Sweden by Svensk Kärnbränslehantering AB (SKB). The facility should be operational in 2023.

Jarno explains:
The actual construction of the Onkalo shafts and main tunnels started in 2004 and ended in 2012. During these years, Posiva also built an Onkalo research facility. At the time of our visit to the facility, Posiva started building and excavating the final nuclear waste placement tunnels. The officials gave the permit to build nuclear waste disposal facilities in 2015, and the construction works began in 2016. Posiva will be building the world`s first safe and efficient nuclear waste disposal plant ever.
The Project
In 1994, parliament amended the Finnish Nuclear Energy Act to specify that all nuclear waste produced in Finland must also be disposed of in Finland. The Finnish government selected Olkiluoto in 2000 as the terminal placement site for a long-term underground storage facility for nuclear fuel spent in Finland. The facility, named “Onkalo” (meaning “small cave” or “cavity”), is being built in the granite bedrock at the Olkiluoto site, about five kilometers from the nuclear power plants. The municipality of Eurajoki issued a building permit for the facility in August 2003. Excavation began in 2004.
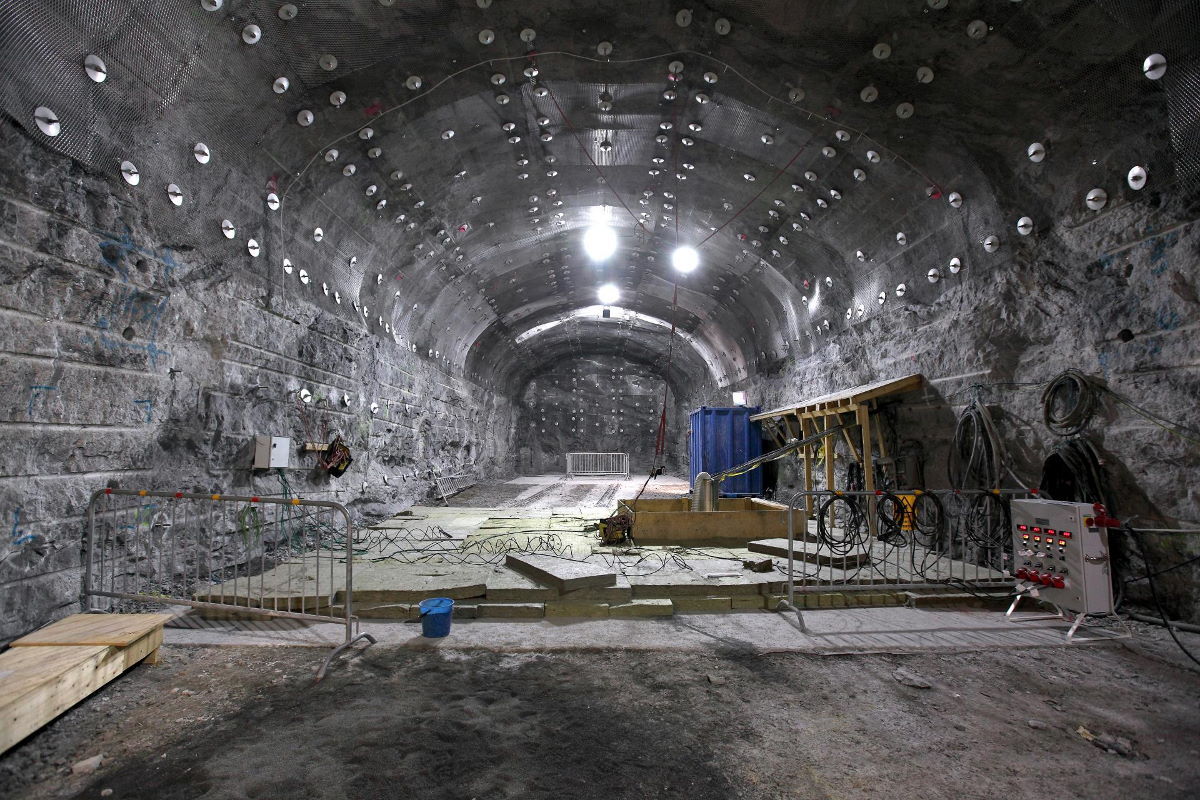
About the challenges of building the facility, Jarno comments:
At the general level, the main challenges in this project have been that we are making the world’s first facility of this kind. So, we are setting an example and standard to the rest of the world that nuclear waste can be safely and efficiently disposed of into the stable bedrock.


Construction of Onkalo
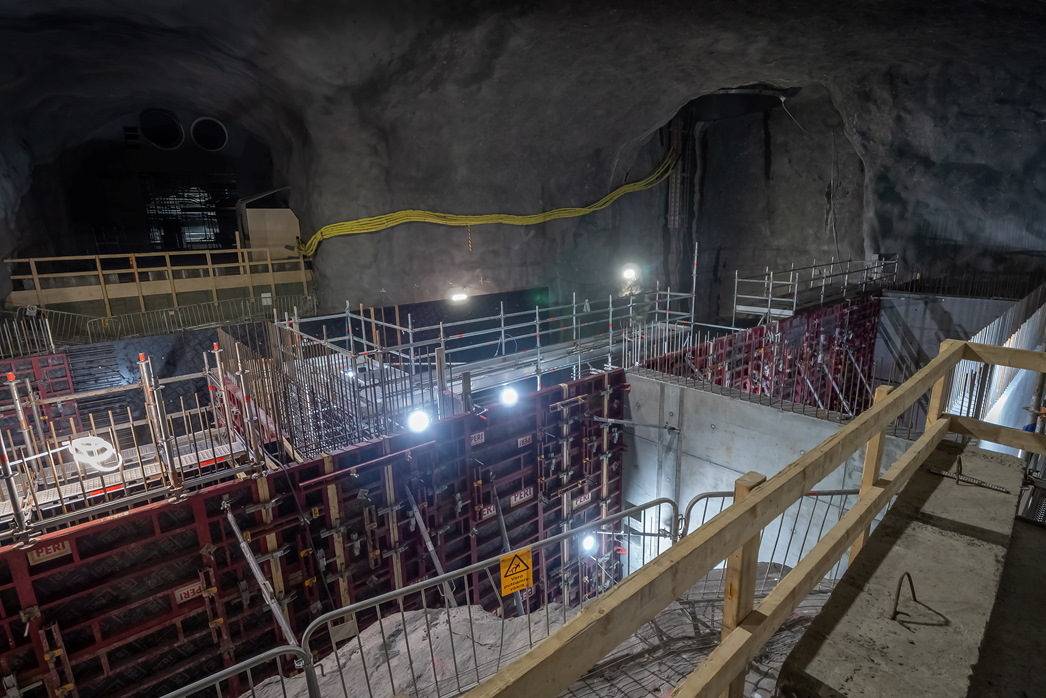
The entire construction and disposal will take about 100 years. Then the premises will be closed. When the facilities are ready, the tunnels’ total length will be about 50km and have a total volume of approximately 1.5 million cubic meters. According to the plans, 6,500 tonnes of spent nuclear fuel will be finalized, which means over 3,000 copper capsules.
Jarno explains.

Building the facility is a vast project and demands specific kinds of tools and equipment. The four shafts in the facility are almost 0.5 km deep. Several works needed to be carried out inside the shafts and on the shaft walls.
Hybrid hoist + mast climber
In assembly work inside the personnel shaft, Posiva is using a Scanclimber hybrid hoist-work platform SC2000. The product was custom-built according to Posiva’s requirements. The SC2000 hoist-work platform is a hybrid of a hoist and a mast climber (MCWP). Posiva wanted a “platform” in the personnel shaft from which to assemble the steel frames and do the HVAC work.

In addition to the shaft platform Posiva, they also needed a device to transport people and material. So based on this idea, the SC2000 was developed.
On the lower floor (1) is a “˜standard” hoist with a sliding door and access in and out on any floor.
On the (2) upper floor of the SC2000 is a work platform where personnel can work and access the shaft walls.
The platform climbs up to 480m and has a maximum capacity of 2000kg. But they also needed a device to transport people and materials.
Jarno says:
In personnel shaft, we use the Scanclimber mast platform, from which the shaft fitting works are performed. We also use the passenger hoist section (floor) of the platform for supportive transportation tasks before we install the actual passenger elevator.
and continues:
Scanclimber’s work platform-hoist combination is used in the personnel shaft for equipment- and HVAC-installations. After their implementation, the actual passenger elevator can be installed in the shaft. The guides for the final passenger lift are also installed from the Scanclimber work platform. After the installation of the guides and HVAC. Posiva will dismantle the platform at the turn of 2022- 2023, and we’ll install a standard counterweighted passenger lift in the shaft.
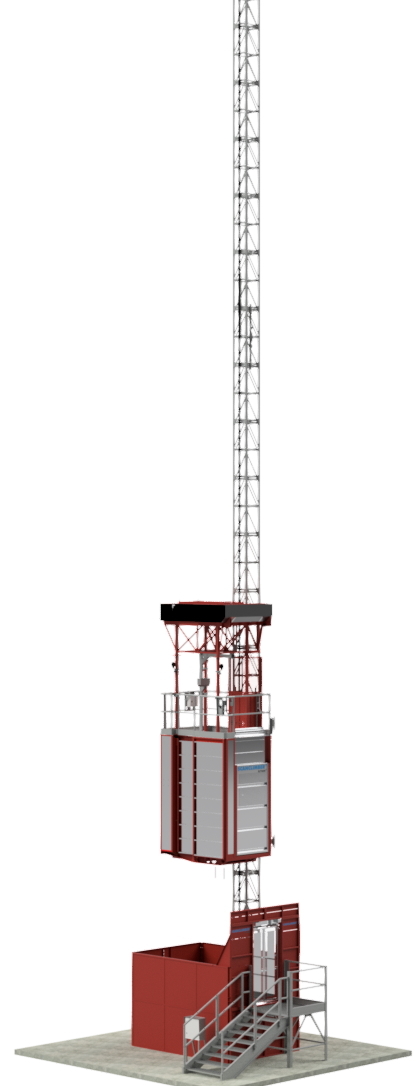
Posiva considered an Alimak-type hoist at the beginning of the project but found no hoist suitable for their needs on the market. That is why they decided on a customized Scanclimber hybrid platform.
The work platform’s primary task is to help in the installation of steel frames inside the shaft. The steel frames are 10-meter-high pre-assembled elements. They are lowered down into the shaft by a crane and installed from the platform. During installation, the steel elements are bolted together and to the shaft wall.
The SC2000 mast will grow as work progresses. The mast sections are transported up with the work platform and installed from the platform with a Scanclimber standard Mast Assembly Crane Arm.
Posiva utilizes the hoist-work platform to install other parts in the shaft, like final personnel lift guiding frames, electrical installations, cabling, lighting, piping, safety, and emergency equipment, etc.
The hoist-work platform is a functional unit and consists of the following main components shown in the picture:
- mast base,
- hoist cage,
- work hoist platform
- protective roof
- drive unit
- landings I and II,
- mast with anchoring,
- cable guide system,
In the shafts -project, there are two, approximately 400-meter vertical shafts that needed to be strengthened and equipped in a way that the final personnel lifts can be safely installed. This has also been a pretty challenging project for myself.
Jarno concluded.
Close to the end of the shaft project, Jarno is satisfied with the platform:
Scanclimber’s work platform has met the expectations placed on it very well. The challenge at first was that the radio control signal from the platform did not work in an almost 500-meter-deep shaft in the bedrock. But when the radio control was replaced with a cable and the control system has worked just fine.
Jarno concludes.